Deltamethrin products can look, work and perform in many different ways. But why so much variation? It comes down to the three main factors that influence the performance of a suspension concentrate deltamethrin formulation. These factors are particle size, plant hygiene and rheology. In this second article in the series we’ll explore the role of plant hygiene and its importance in formulation performance.
What is a formulation plant?
A formulation plant is a facility where pesticides or other chemical formulations are produced. This involves blending and mixing various chemicals in specific proportions to create the desired end product.
What is formulation plant hygiene?
Formulation plant hygiene refers to the practices and measures implemented to maintain a clean and sanitary environment within a facility where products are formulated, processed or manufactured. This is especially important in pesticide manufacture where the quality and safety of the products are of utmost importance. Proper hygiene ensures that the end products are free from contamination and meet pest managers’ required standards and expectations. Key aspects of formulation plant hygiene include facility cleanliness, workers’ hygiene, waste management, quality control, training and education, and compliance with regulations.
Have you ever opened a new bottle of pesticide and found it smelled off, with a raw sewage or awful smell? Have you contacted a manufacturer to complain about the smell of a product only to be told that the product has been tested and that it is ‘within specification’?
This means the manufacturer has sent a sample to be tested and the laboratory has confirmed the amount of active ingredient is present at the level stated on the product label. For example, if a deltamethrin product states that there is 10 g per litre, the laboratory will confirm that the sample submitted contains the required amount of deltamethrin. Therefore the product is assessed as being ‘within specification’.
So, what is the awful smell emanating from your new bottle of product?
Foul-smelling odours are commonly the result of microbial activity. This is a typically result of poor plant hygiene and/or insufficient biocides in the formulated product. Microorganisms, such as bacteria or fungi, can contaminate pesticides and initiate biodegradation processes. The metabolic activities of these microbes produce volatile organic compounds that cause the characteristic bad smell.
My product smells bad – so what?
Pesticides with microbial contamination can pose several issues, ranging from product quality concerns to health and safety risks. Some of the key issues for pest management professionals:
- Reduced product efficacy: microbial contamination can alter the chemical composition of the pesticide, leading to a loss of effectiveness and potency. This is particularly concerning because of the precise dosage that is required to attain the desired pest control outcome.
- Product degradation: microorganisms break down essential chemical compounds through enzymatic actions, causing the pesticide to degrade prematurely. This results in shorter self-life and reduced usability.
- Foul odour and appearance: microbial contamination leads to the production of off-smells and unpleasant odours, making the pesticide unappealing to customers.
- Inconsistent product quality: microbial contamination can result in uneven distribution of active ingredients, leading to variations in product quality from one batch to another. This is a result of the microbes consuming the thickeners holding the active ingredient in suspension in the formulation.
- Health and safety concerns: some microbial contaminants can produce toxic substances or allergens, posing health risks to users and consumers. For example, some mould spores and bacterial toxins can cause respiratory issues, allergic reactions and occasionally even worse consequences.
Figure 1 is an independent laboratory report of a cheap generic 10 g/L deltamethrin product that was sent to Sundew Solutions for analysis after a pest manager was told that his product was within specification. Not satisfied with the generic company’s response the pest manager reached out to the Sundew team for insights into why his product smelled bad out of the bottle.
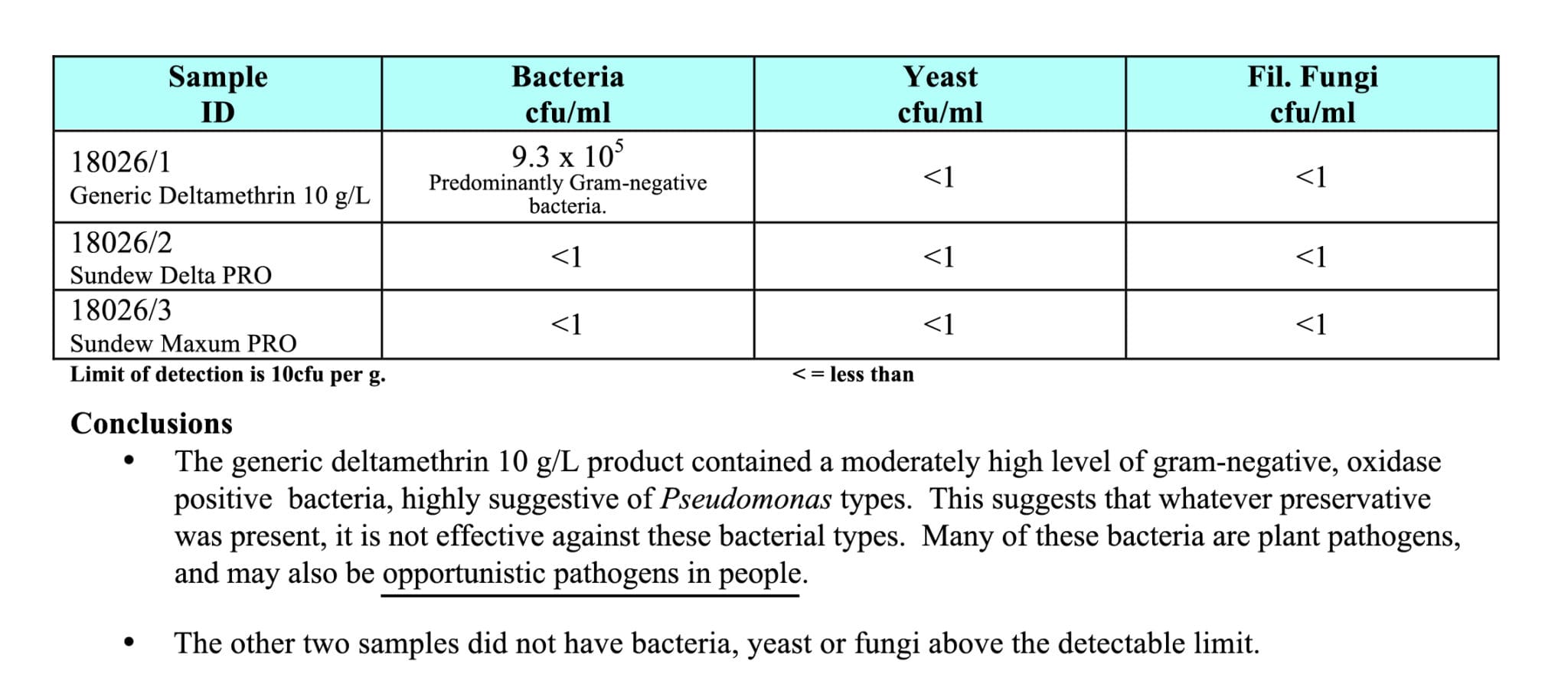
The sample was submitted to an independent laboratory that screened for bacterial, yeast and fungi contaminations. The cheap generic deltamethrin was found to contain 930,000 colony-forming units of bacteria per 1 ml of product. This is incredibly alarming for our industry.
The laboratory technician went on to state, “The product contained a moderately high level of gram-negative, oxidase positive bacteria, highly suggestive of Pseudomonas types [shown in main picture, above]. This suggests that whatever preservative was present, it is not effective against these bacteria types. Many of these bacteria are plant pathogens, and may also be opportunistic pathogens in people.”
What happens when a formulation plant experiences a microbial contamination in its production facility?
This is a major headache for formulation plants. Passing a disinfectant or cleaning chemical through production equipment is generally not sufficient to eliminate the issue. The only way to be 100% sure is to disassemble the equipment and physically scour, disinfect and clean from one end to the other. This necessitates shutting down whole production lines for large blocks of time, which is a significant challenge for generic and large volume manufacturers, as they can’t avoid the lost production time. When multiple batches of different products are processed through the same equipment, they can all become contaminated.
In Australia, pest management professionals have experienced products with ‘bad odour’ from completely different chemical companies. However, if you traced the product back to the manufacturing facilities you can often find they are being processed at the one common toll manufacturer site, where every batch of product going through the line is being cross-contaminated with microbial elements, one after the other.
Quality plant hygiene practices
To significantly reduce the chance of such issues occurring during the manufacture of Sundew DeltaPRO 25 there are stringent quality control measures and good manufacturing practices to relevant industry standards in place. Every batch of product is tested by an independent laboratory and monitored for microbial contamination.
Additionally, during formulating there is implemented effective cleaning and sanitisation practices to minimise the risk of plant hygiene becoming an issue with its DeltaPRO 25 Suspension Concentrate or any of its other quality formulations.
In the next issue of Professional Pest Manager magazine we’ll explore the topic of formulation rheology in relation to product stability when creating the ultimate deltamethrin insecticide.
David Priddy, Chief Executive Officer, Sundew Solutions
Read Part 1 of this series that looks at the role of particle size or Part 3 that explores the importance of rheology in a deltamethrin formulation.
Published Professional Pest Manager Magazine, September 2023. The second of a three-part series looking at the science behind deltamethrin formulations. Written by David Priddy, CEO of Sundew Solutions.
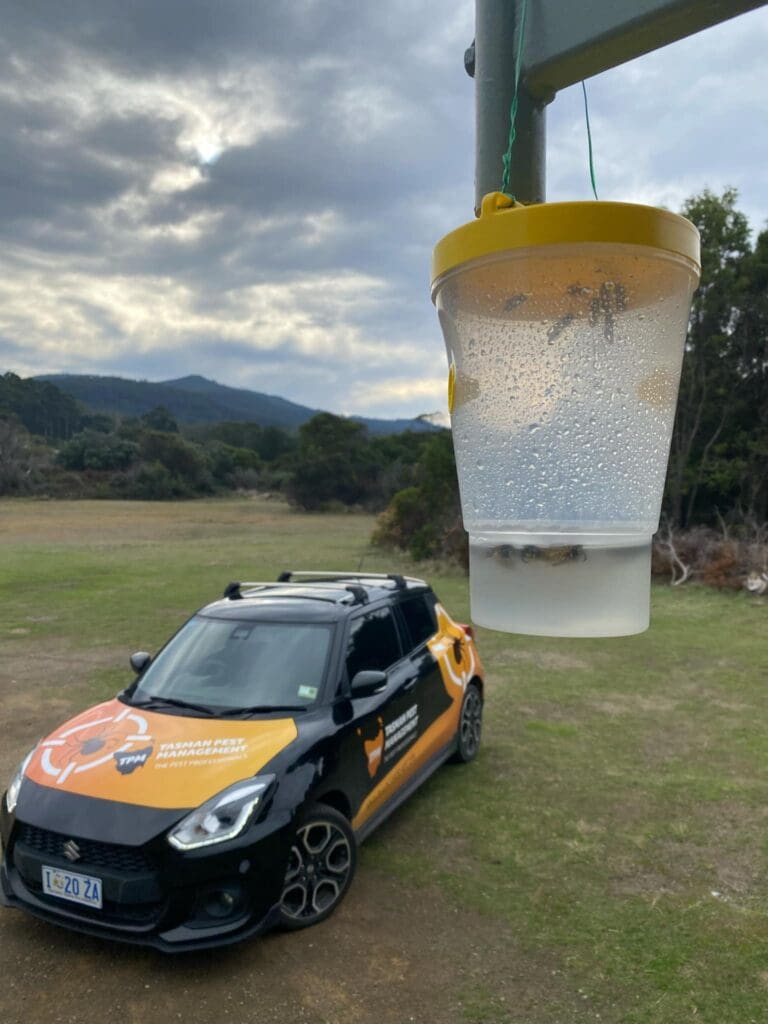
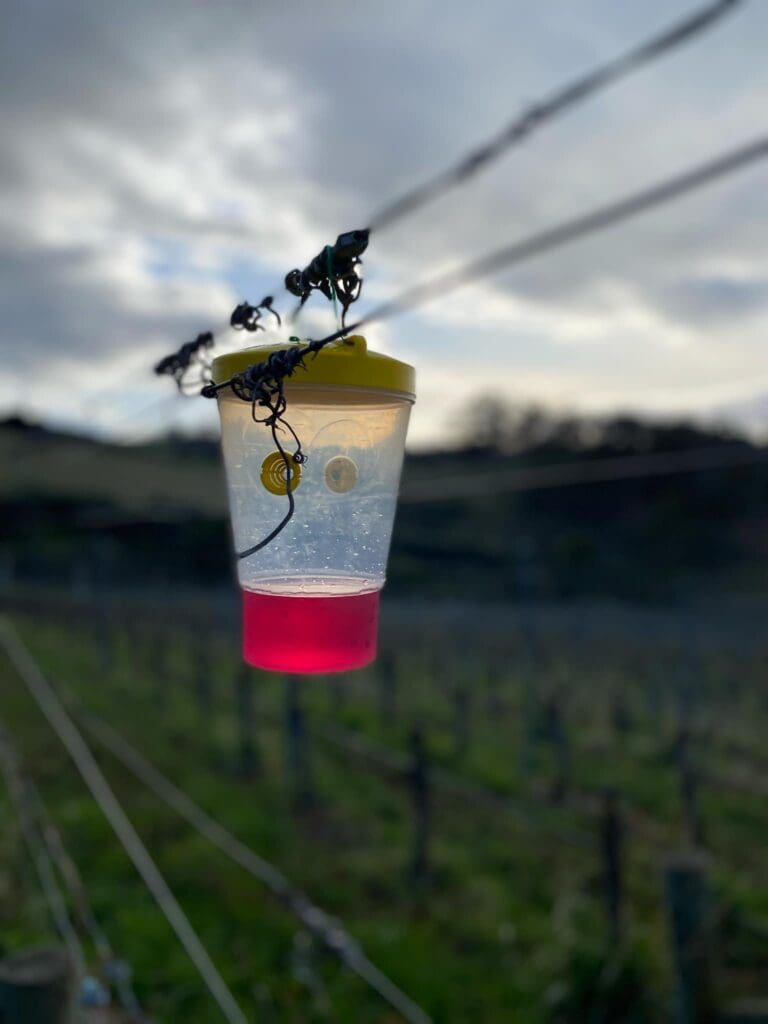
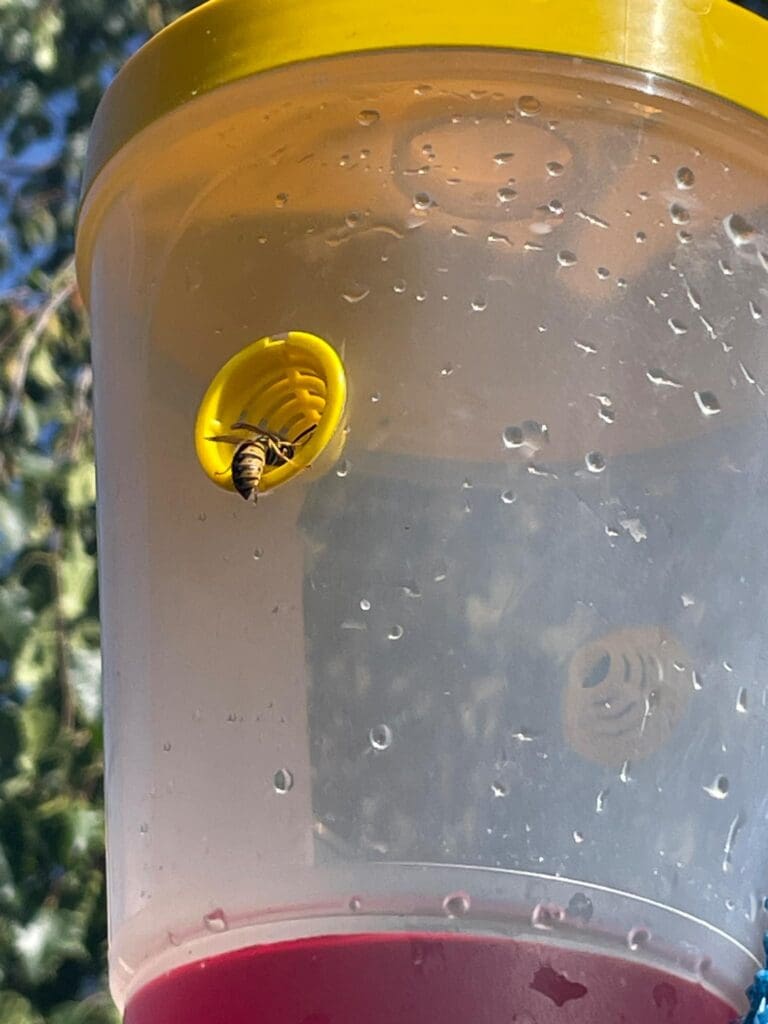