Have you ever wondered why so many deltamethrin products can perform, look and work in so many varying ways? It comes down to the three main factors that influence the performance of a suspension concentrate deltamethrin formulation: particle size, plant hygiene and rheology. In this first article in the series we’ll explore the role of particle size, with hygiene and rheology being the subject of parts two and three.
Particle size – what’s the BIG deal?
The particle size of the active ingredient is one of the most important properties that will influence how a product will perform.
When a deltamethrin product is being formulated by a chemical manufacturer, they start with raw active ingredient – in this case, deltamethrin.
In its raw form it is a coarse, non-soluble white powder. In this raw form, deltamethrin particles are too large to be put into a suspension concentrate product for pest managers to use because it will block spray nozzles, leave sediment in the tank and result in callbacks. Therefore at the formulation plant, the raw deltamethrin is put into a piece of equipment known as a bead mill.
Small ceramic, glass or metal beads are agitated inside the mill chamber to aid deltamethrin particle size reduction, making it more suitable for use in a finished formulation.
Something to note: particle size is not an ‘absolute’ measurement. That is to say, when undergoing the sheer forces in a bead mill, the active ingredient will have a broad range of particle sizes in a mix. The longer a product is milled, the finer/smaller the relative particle size mix will be. Conversely, the shorter the time a product is mixed, the larger the spectrum of particle sizes.
So what’s the big deal about small or large particle size? If you milled deltamethrin active and made a finished product where the average particle size was 25.6 μm, when you mixed this up in your tank and sprayed onto a surface you would have 1 particle of deltamethrin per mm2. If you worked the deltamethrin active in the mill until you achieved a smaller average particle size of 12.8 μm, and then mixed this in your spray tank and applied onto a surface, you would have 8 particles of deltamethrin per mm2. If you milled the deltamethrin active a little longer and achieved an even smaller average size of 1 μm, and then mixed it in your tank and applied to a surface, you would find there would be 16,852 particles per mm2.
If you were an insect walking across the surface in each of these three particle size scenarios, which do you think is most likely to coat an insect and therefore have greater efficacy over the others?
While smaller particles are advantageous for flushing and fast knockdown, they are more susceptible to breaking down due to environmental influences – pH, temperature, rain and UV light. Bigger particles are advantageous for residual control. The larger mass of the particle provides better insulation from environmental influences. However, if you make the particles too big you will end up with visible surface residues, poor residual (the particles cannot penetrate into the insect exoskeleton), wear and tear on equipment (abrasion on tips as the product flows through them), and uneven availability of active.
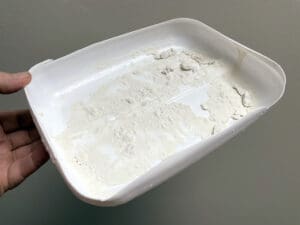
So what is the correct particle size?
The correct answer depends on the result you want your finished product to achieve. If the chemical manufacturer wishes to create a product that has amazing flush and knockdown (and no residual action) they will mill the deltamethrin particle to a very small size spectrum.
Conversely, if the manufacturer wishes to create a product with long residual control, they will mill the particles to a larger size. Some products have both small and large particles, to get the knockdown and residual, but they don’t always get it right, with particles sometimes too big to penetrate the insect cuticle (Figure 2).
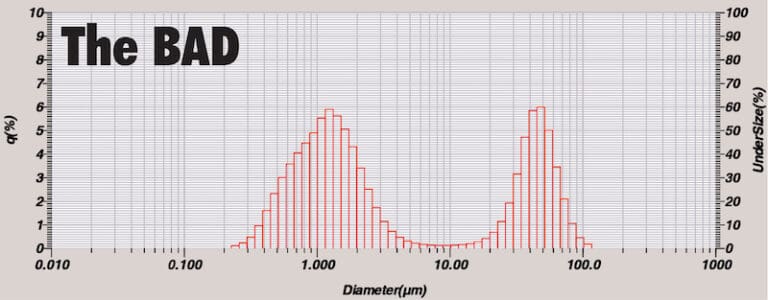
Some products have predominately small particles, while others have all larger. Indeed sometimes the particles are so large they are visible to the naked eye and cause application issues (Figure 3). This is despite the fact that they all have deltamethrin as their active ingredient.
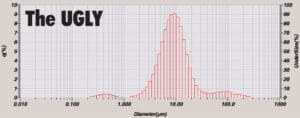
Controlled particle technology
Sundew Solutions’ DeltaPRO 25 Suspension Concentrate has a bi-modal particle size spectrum – that is to say, it contains a mix of both small and large particle distributions. Importantly, the bi-modal particle sizes chosen are crafted batch by batch to a specific predetermined particle distribution. This ensures the highest formulation standard – a standard the pest management professionals can stake their reputations on.
Sundew products that have this bi-modal (two particle size distributions) formulation technology are referred to as having ‘controlled particle technology’.
This is smart formulation science in that it offers the perfect bi-modal blend of tiny sub-micron particles that have been shown to give a rapid knockdown, while a complement of larger particles provides excellent residual control on even the most porous surfaces (Figure 1). This gives these Sundew products outstanding all-round performance – fast acting on the largest range of surfaces with long residual performance.
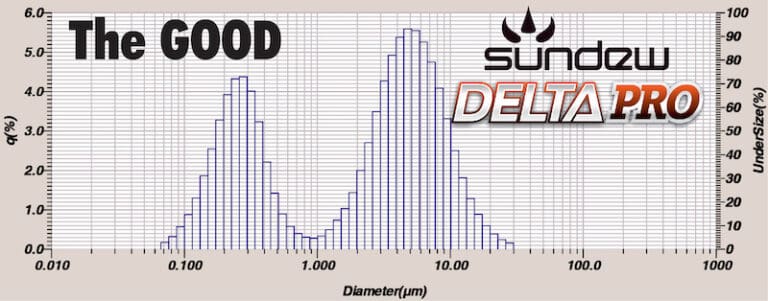
Bad particle sizes, not poor actives
Over the years, pest management professionals have told us how they’ve switched to using a product with a new active, on the basis that the performance was better than their previous product that used an older active. However, it’s important not to assume that products using the same active will have the same performance; they don’t. Deltamethrin may be an older active but it is still capable of delivering great performance in the right formulation. Sundew Solutions understands that particle size is the critical factor in the performance of SC formulations, which is why DeltaPRO 25 performs so well. So, when selecting a product ask questions about the formulation and not the active.
David Priddy, Chief Executive Officer, Sundew Solutions
Read Part 2 of this series that looks at the role of plant hygiene or Part 3 that explores the importance of rheology in a deltamethrin formulation.
Published Professional Pest Manager Magazine, June 2023. The first of a three-part series looking at the science behind deltamethrin formulations. Written by David Priddy, CEO of Sundew Solutions.
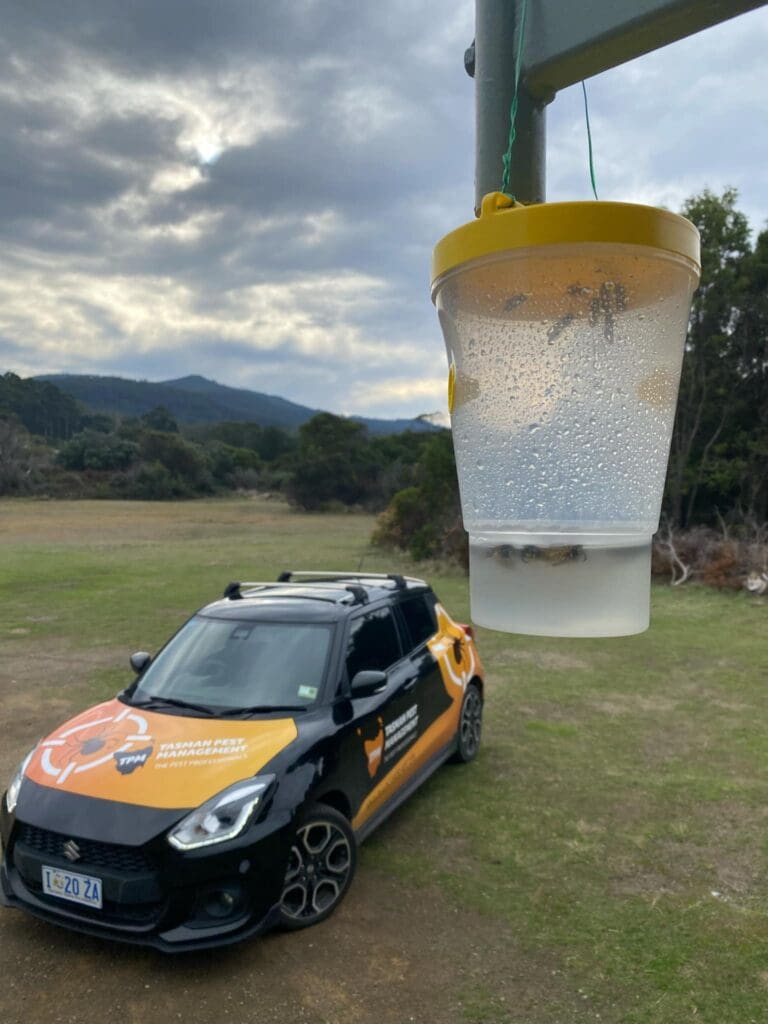
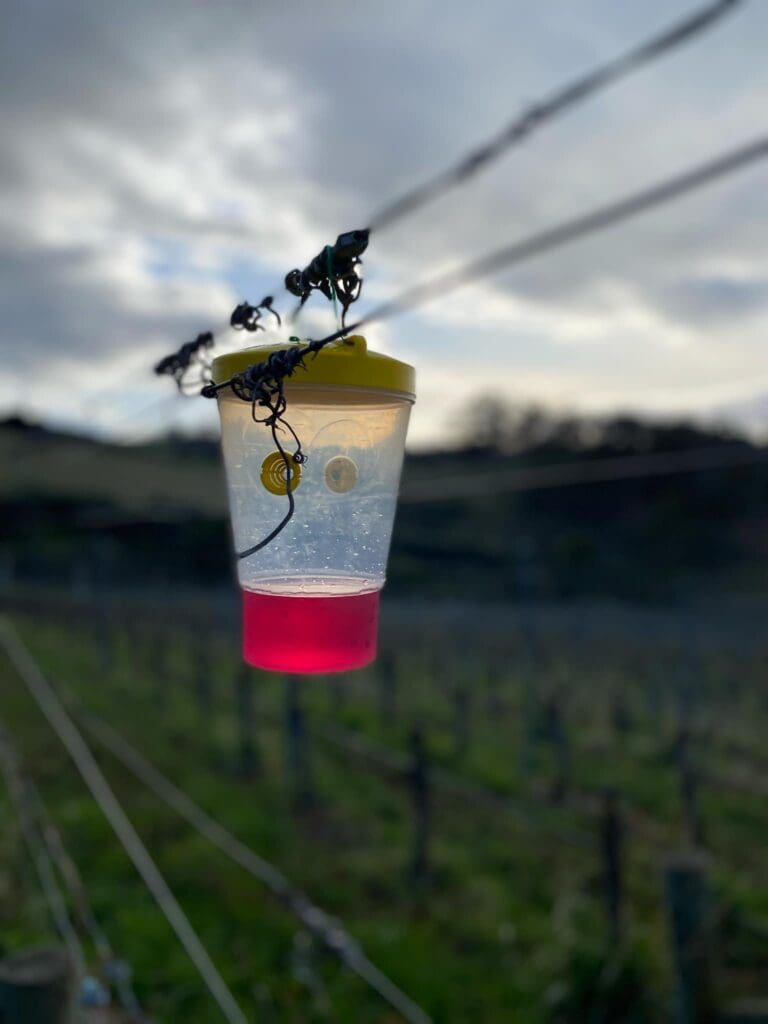
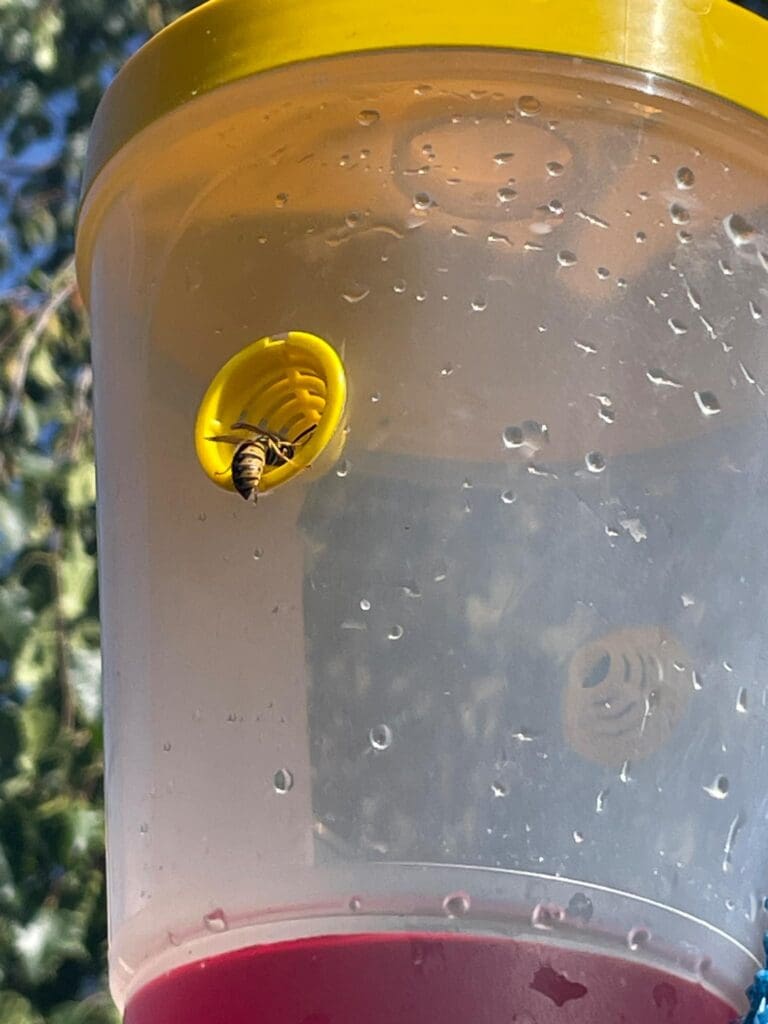